Emerging Applications of Semi-Solid Die Casting in Automotive Lightweighting
Core keywords: semi-solid die casting, automotive lightweighting
As automakers push forward with lighter, more energy-efficient vehicle designs, semi-solid metal casting is increasingly being recognized as a next-generation solution for structural part production. With its ability to deliver superior material flow characteristics, minimal internal porosity, and increased strength, semi-solid die casting stands out as a highly effective method for manufacturing load-bearing components in electric and hybrid vehicles. These performance advantages make it a strategic asset in achieving automotive lightweighting goals without compromising structural integrity.
1. What Is Semi-Solid Die Casting?
Semi-solid die casting is a process where a partially solidified metal mixture—often described as a "slurry"—is carefully filled into a mold cavity under precise thermal and flow control, enabling better formability and reduced defects. Compared to traditional high-pressure die casting, the thixotropic nature of the slurry allows:
-Lower filling speed and pressure
-Reduced shrinkage and porosity
-Excellent surface finish and dimensional accuracy
This positions SSM casting as a preferred method for fabricating high-load components like suspension joints, transmission casings, and integral structural elements within the vehicle chassis.
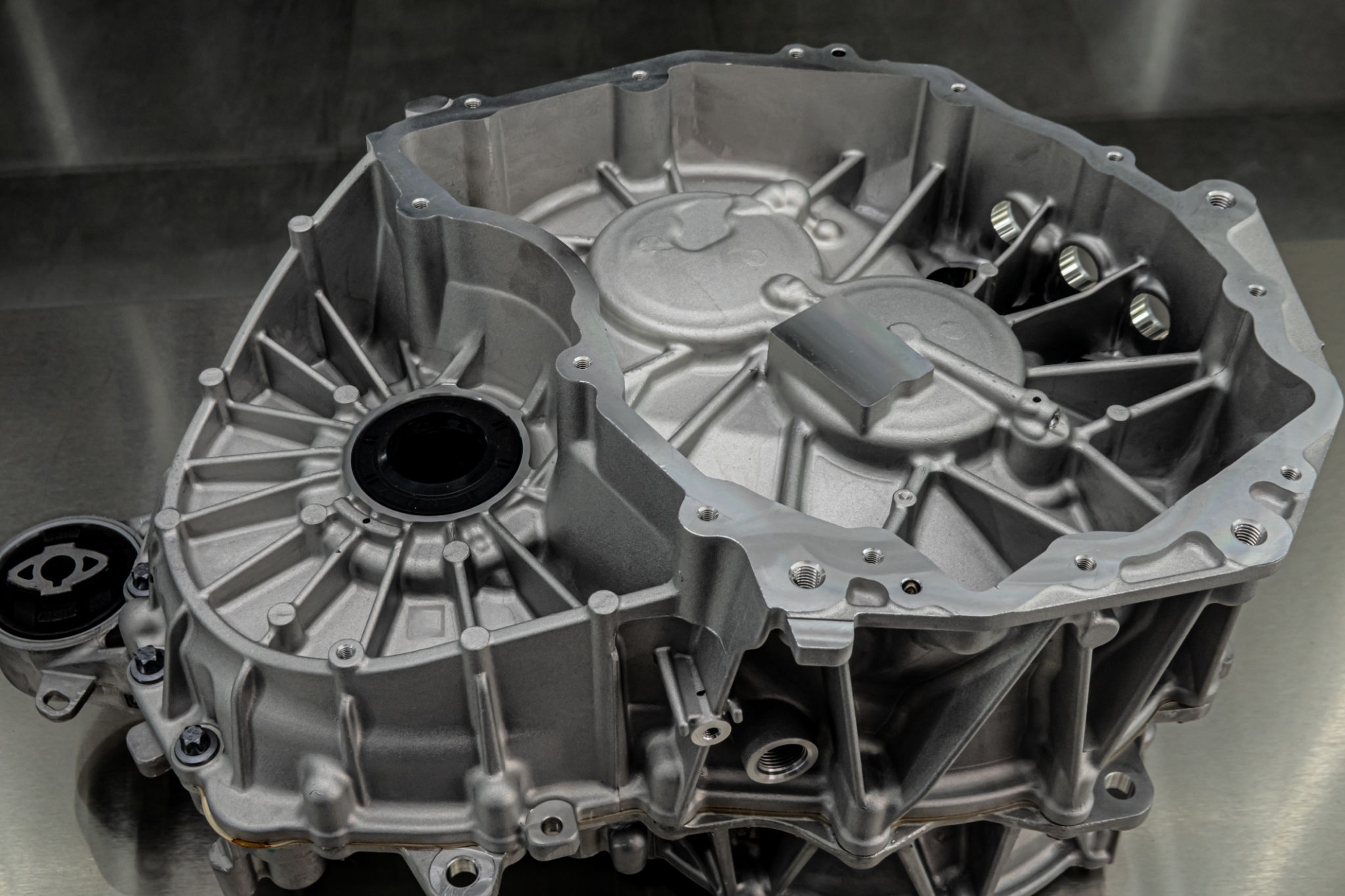
2. Horizontal Comparison: Traditional Die Casting VS Semi-Soild Die Casting
Feature | Traditional Die Casting | Semi-Solid Die Casting (SSM) |
Injection Pressure | High (>100 MPa) | Moderate (30–80 MPa) |
Porosity Issues | Moderate to High | Very Low |
Mechanical Properties | Standard | 10–20% Higher Yield Strength |
Wall Thickness Capability | 2.5–3.0 mm | <2.0 mm possible |
Material Utilization | Less | More |
Cooling Rate Faster | Faster | Slower, more uniform |
From this data, it's clear that semi-solid die casting outperforms traditional methods in structural integrity and thickness reduction, both critical for automotive lightweighting.
3. Material Trends: Magnesium and Aluminum Alloys
Aluminum Alloys
Aluminum alloys such as A356 and A357 have become common choices in SSM technology due to their compatibility with the process. Their combination of low density and excellent corrosion resistance makes them ideal for use in engine parts, EV casings, and battery enclosures.
Magnesium Alloys
As the lightest structural metal, magnesium is increasingly used in semi-solid die casting to replace steel and aluminum. Compared to aluminum, magnesium parts are 33% lighter while still maintaining acceptable strength levels for chassis components.
🔍 Example: A magnesium-based steering wheel frame weighs 1.2 kg vs. 1.8 kg for aluminum—a 33% reduction.
4. Why It Matters: Sustainability and EV Adoption
The rise of electric vehicles (EVs) is pushing OEMs to cut every gram of unnecessary mass. Lighter vehicles directly correlate with longer battery range and lower energy consumption. By adopting semi-solid die casting, manufacturers can:
- Consolidate multiple parts into one (reducing welding or fastening)
- Use less material for equivalent strength
- Improve thermal conductivity for battery and motor cooling systems
5. Conclusion: A Strategic Path Forward
In the race towards automotive lightweighting, semi-solid die casting stands out as a robust, scalable, and sustainable solution. It bridges the gap between the precision of forging and the versatility of casting—unlocking design flexibility without compromising strength.
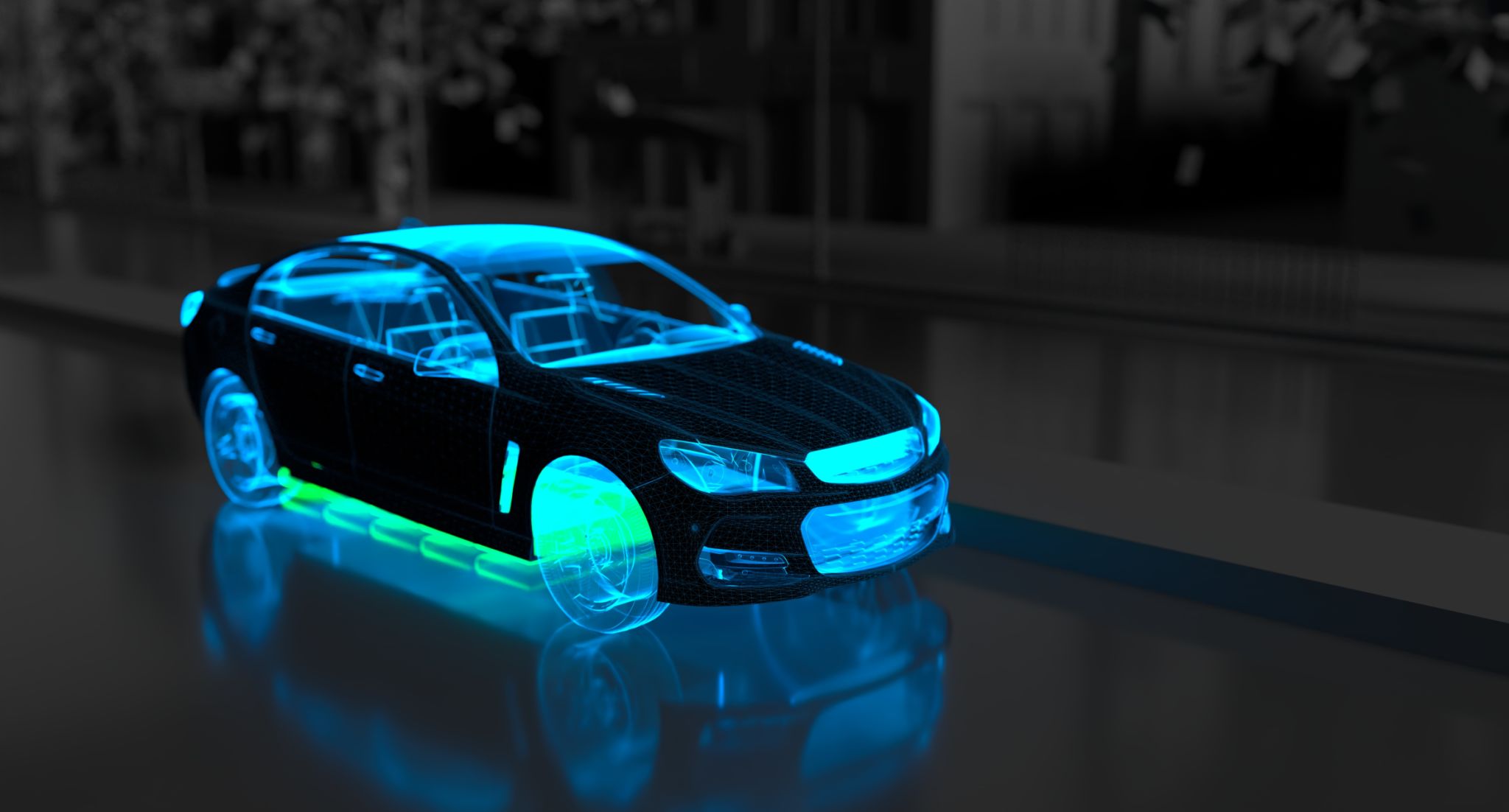
Manufacturers aiming to stay competitive in the EV and next-gen mobility sectors must consider integrating SSM casting in their production pipeline now—not later.
🚀 Unlock the Future of Lightweight Manufacturing with SHD Precision Diecasting
At SHD Precision Diecasting, we specialize in semi-solid die casting services tailored for the automotive, electronics, and industrial sectors. With over a decade of manufacturing experience, our expert engineering team supports your transition to lightweight structural components—whether it's aluminum or magnesium alloys.
From design consultation to precision mold development and mass production, we offer full-spectrum solutions that help you reduce weight, improve performance, and stay ahead in a competitive EV market.
✅ Capabilities include:
- Semi-solid die casting (SSM) for complex geometries
- Alloy consultation and material optimization
- CNC secondary processing & quality assurance
- ISO/IATF-compliant production systems
📩 Let’s start your lightweighting journey today.
Contact us to discuss your project or request a quote at www.shd-precision.com
SHD Precision Diecasting — Where Innovation Meets Industrial Precision.