How to Choose Between Sandblasting, Electroplating and Anodizing?
In the realm of industrial manufacturing, surface finishing techniques like sandblasting, electroplating, and anodizing play pivotal roles in enhancing product durability, esthetics, and performance. Understanding the nuances of each method is crucial to selecting the most suitable process for your specific application.
Sandblasting: Surface Preparation and Cleaning
Sandblasting utilizes high-velocity abrasive particles to effectively strip away contaminants or create a uniform surface texture on various materials. It's widely used for removing rust, paint, or other contaminants, providing a clean slate for further processing.

Key Benefits:
-Efficient removal of surface impurities
-Prepares surfaces for painting or coating
-Can create desired surface textures
According to Market Insight we knew: the global sandblasting media market is valued at approximately USD 9.72 billion in 2024 and is projected to reach USD 19.91 billion by 2034, growing at a CAGR of 7.43%.
Electroplating: Enhancing Surface Properties

Electroplating involves applying a thin layer of metal onto a substrate through the use of an electric current, enhancing both the surface properties and appearance of the base material.This method is widely applied to strengthen resistance to corrosion, minimize surface friction, and provide a polished, decorative finish.
Key Benefits:
-Improved corrosion and wear resistance
-Enhanced electrical conductivity
-Aesthetic appeal with various metal finishes
According to a recent market analysis, the global electroplating sector is projected to attain a value of USD 17.35 billion by 2024, reflecting its sustained industrial relevance. With steady demand across the automotive, electronics, and aerospace sectors, the market is forecasted to expand to USD 24.03 billion by 2033, reflecting a consistent annual growth rate of 3.51%.
Anodizing: Durable and Decorative Finishes
Through an advanced electrochemical technique, anodizing enhances metal surfaces by forming a robust oxide layer, significantly improving resistance to corrosion and wear while offering aesthetic versatility. It's particularly effective for aluminum components.
Key Benefits:
-Enhanced corrosion and wear resistance
-Improved surface hardness
-Ability to add vibrant colors for aesthetic purposes
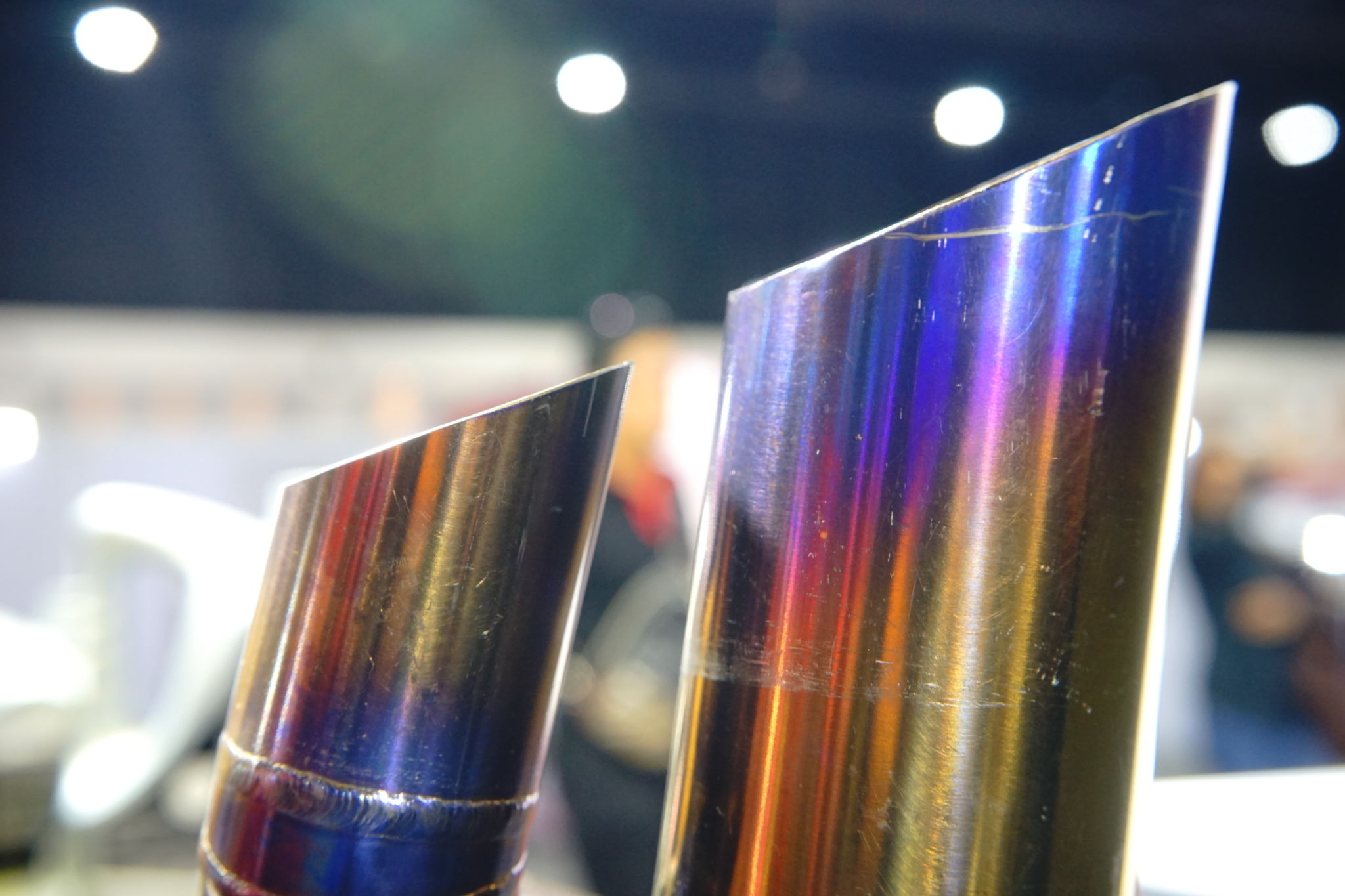
The demand for metal anodizing continues to rise, with the market valued at USD 3.10 billion in 2024. Driven by increasing applications in the consumer electronics and architectural sectors, it is anticipated to surpass USD 5.02 billion by 2033, supported by a healthy CAGR of 5.8%.
Comparative Overview
Process | Primary Use Cases | Advantages | Considerations |
Sandblasting | Surface cleaning and preparation | Quick and effective contaminant removal | May roughen surfaces; requires containment |
Electroplating | Corrosion resistance, aesthetic finishes | Durable, conductive, decorative | Involves hazardous chemicals; environmental regulations |
Anodizing | Protective and decorative aluminum finishes | Hard, corrosion-resistant, colorful | Limited to certain metals; initial setup cost |
Making the Right Choice
If your primary goal is to remove surface contaminants or to prepare materials for subsequent coatings, sandblasting remains one of the most efficient and cost-effective methods available.
-Material Compatibility: Anodizing is ideal for aluminum, while electroplating suits a variety of metals. Sandblasting is versatile across many materials.
-Desired Properties: For corrosion resistance and esthetics, electroplating and anodizing are preferable. When it comes to efficient surface cleaning and pre-treatment, sandblasting offers a reliable solution across diverse industrial applications.
-Environmental and Safety Concerns: Anodizing is generally more environmentally friendly compared to electroplating, which uses hazardous chemicals.
-Cost and Time: Sandblasting is typically quicker and less expensive, whereas anodizing and electroplating involve more complex setups and processes.
By understanding the specific requirements of your project and the characteristics of each surface treatment method, you can make an informed decision that ensures optimal performance and longevity of your products.
Conclusion
Choosing the optimal surface finishing process requires careful evaluation of material types, functional requirements, and desired aesthetic outcomes specific to your project. If you prioritize durability and eco-friendliness for aluminum parts, anodizing is ideal. For aesthetic metallic finishes, electroplating is the best option. When surface preparation or cleaning is required, sandblasting leads the way.
Ensure optimal results for your metal components by working with experts in surface finishing. At SHD Precision Diecasting, we provide industry-leading OEM services, covering sandblasting, electroplating, anodizing, and more—designed to enhance durability, appearance, and performance.