Porosity in Die Casting: Common High-Pressure Die Casting Defects and Effective Control Methods
Porosity in die casting remains a major quality concern in modern manufacturing, often leading to high rejection rates and increased production costs. In high-pressure die casting (HPDC), where molten metal is injected into a mold at high speed and pressure, even slight turbulence, gas entrapment, or solidification imbalance can lead to tiny internal voids or bubbles—commonly known as porosity. These defects may seem minor but can seriously affect part strength, sealing performance, and customer acceptance.
For industries such as automotive, consumer electronics, and aerospace, porosity is not just a cosmetic flaw—it’s a structural risk. This article explores the root causes of high-pressure die casting defects, with a focus on porosity, and provides actionable porosity control methods to help engineers and quality managers produce better castings.
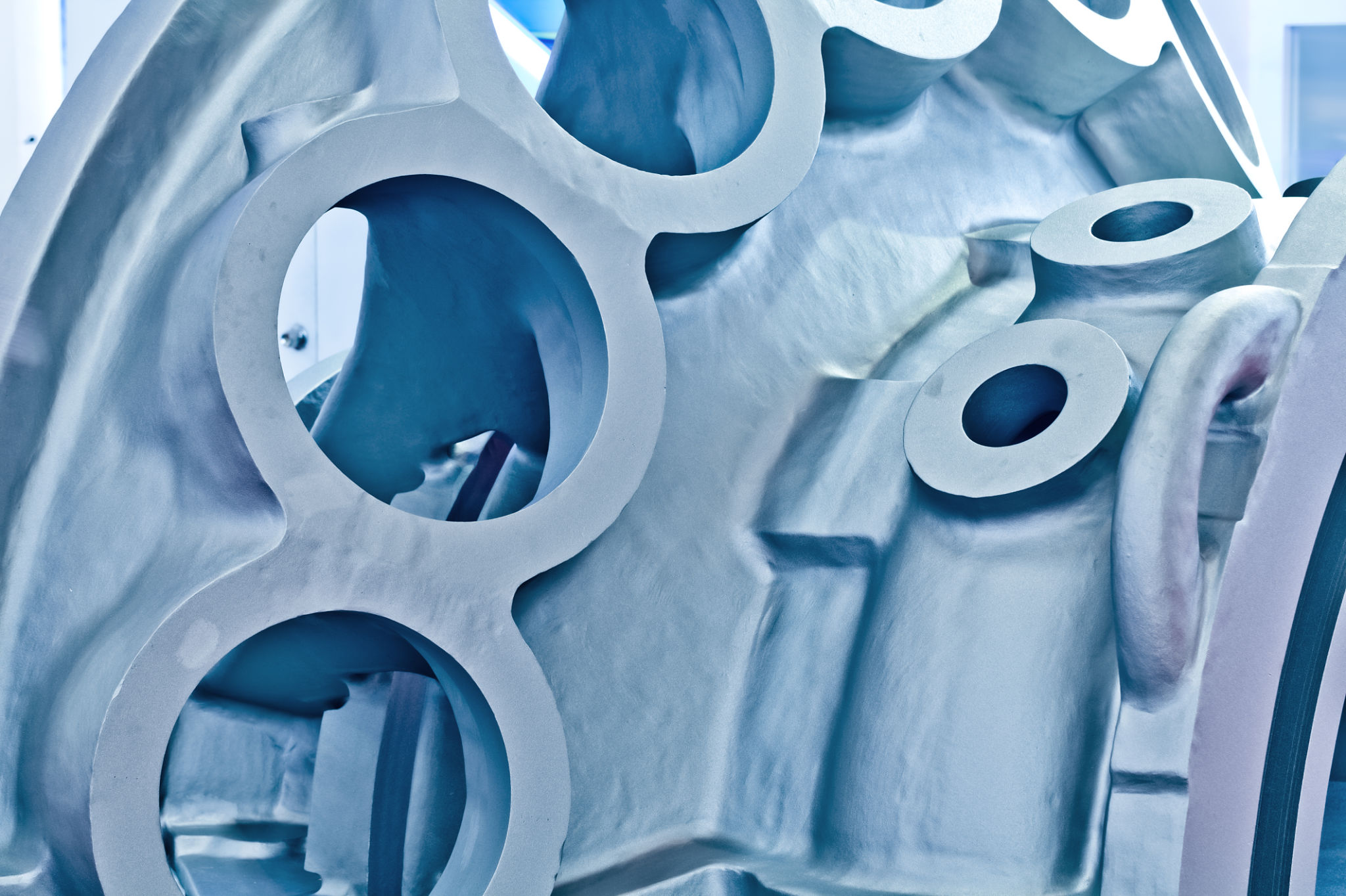
What Is Porosity in Die Casting?
Porosity in die casting describes the formation of tiny gas pockets or voids within the metal as it solidifies inside the mold. In HPDC, porosity is typically caused by:
-Air entrapped in the die cavity during injection
-Gas generated by excessive die lubricants or moisture
-Shrinkage during cooling when metal volume contracts
-Poor venting or uneven die temperature
Porosity in die casting can appear as microscopic bubbles or larger cavities and may be randomly distributed or concentrated in specific regions of the part—particularly near thick walls, ribs, or bosses.
High-Pressure Die Casting Defects Related to Porosity
Porosity is considered one of the top five high-pressure die casting defects, often leading to:
-Pressure leakage in hydraulic or fluid-handling parts
-Surface blistering or paint adhesion failure
-Weakening of structural areas, leading to cracks or fatigue
-Weld failure when machining or joining porous areas
Many OEMs have strict porosity tolerance limits, especially in sealing zones or cosmetic surfaces. If not properly managed, porosity can result in part rejection, rework, or costly field failures.
Proven Porosity Control Methods
Here are five key porosity control methods that can be implemented at various stages of the die casting process:
1. Vacuum Die Casting
This technique evacuates air from the mold cavity before injection, significantly reducing trapped gas. It’s ideal for critical components like automotive housings and sealing enclosures.
2. Improved Gate and Runner Design
Optimizing flow paths reduces turbulence during metal filling, minimizing air entrapment. Simulation tools (e.g., MAGMASoft) are often used to design smoother metal flows.
3. Mold Temperature Control
Stable, uniform mold temperatures prevent cold shuts and shrinkage porosity. The use of thermal sensors and controlled water cooling is essential.
4. Metal Purity and Degassing
Using clean alloys and performing degassing (with argon or nitrogen) reduces hydrogen absorption, one of the common causes of gas porosity.
5. Shot Sleeve Lubrication Optimization
In high-pressure die casting, improper lubricant spraying often causes vapor buildup, which contributes to internal porosity in die casting. Controlled dosage and precise cycle timing help avoid excessive gas generation in the sleeve and reduce the risk of porosity-related defects.
Inspection Methods to Detect Porosity
After casting, non-destructive testing plays a crucial role in detecting internal porosity in die casting, ensuring structural integrity before parts move downstream. Methods include:
-X-ray or CT scanning for volumetric porosity analysis
-Pressure leak testing for sealed parts
-Dye penetrant testing for surface-level pores
By combining process control with inspection, manufacturers can ensure long-term quality and customer confidence.
SHD Precision Diecasting: Your Partner in Porosity Control
At SHD Precision Diecasting, we specialize in producing aluminum and zinc castings with strict porosity control. From vacuum-assisted HPDC to in-house X-ray inspection and mold flow simulation, our engineering team ensures that each part meets the highest standards.
Whether you're struggling with porosity in die casting, or need assistance diagnosing high-pressure die casting defects, we offer reliable solutions backed by advanced technology and decades of manufacturing experience.
Conclusion
Porosity remains one of the most critical challenges in die casting—but with proper design, control, and inspection, it can be minimized or even eliminated. Implementing proven porosity control methods not only improves part quality but also enhances brand reputation and long-term cost efficiency.
Need help eliminating porosity from your die-cast parts? Contact SHD Precision Diecasting for expert consultation and precision manufacturing solutions.