How Does Mega Die Casting Subvert the Automotive Manufacturing Industry?
In recent years, with the continuous upgrading of electric vehicle manufacturing technology, Mega die Casting, as a new way of manufacturing automobile structures, has gradually become the focus of heated discussion in the industry. Its core concept is to complete the die-casting of structural parts originally composed of dozens or even hundreds of parts on a super-large die-casting machine at one time, thereby greatly simplifying the process, improving manufacturing efficiency, and reducing the cost of the whole vehicle.
Mega Die Casting: The First Large-Scale Breakthrough in Automotive Manufacturing
Since 2020, Tesla has used giant die-casting parts in the rear chassis of the Model Y model to replace more than 70 original welded parts. The production of this large die-casting part relies on the 9,000-ton die-casting equipment provided by the IDRA Group, which helps it achieve significant advantages in structural weight reduction, manufacturing cycle and vehicle cost. According to Automotive News data, Tesla's vehicle manufacturing time has been shortened by more than 10%, and the cost of a single vehicle has dropped by about US$500.
More car companies join the battle
Not only Tesla, Mega die Casting has become a consensus in the field of automotive die-casting. In its "Trinity" electric vehicle project, Volkswagen plans to adopt an Mega die Casting rear body structure. New Chinese forces such as Weilai, Xiaopeng, and Xiaomi have also invested in the construction of large-scale die-casting production lines. For example, Weilai cooperated with Ningbo Xusheng to introduce IDRA giant die-casting equipment, and Xiaomi Automobile introduced large die-casting machines for chassis die-casting tests during the research and development stage. BYD has developed its own 6,000-ton die-casting equipment and entered the core link.
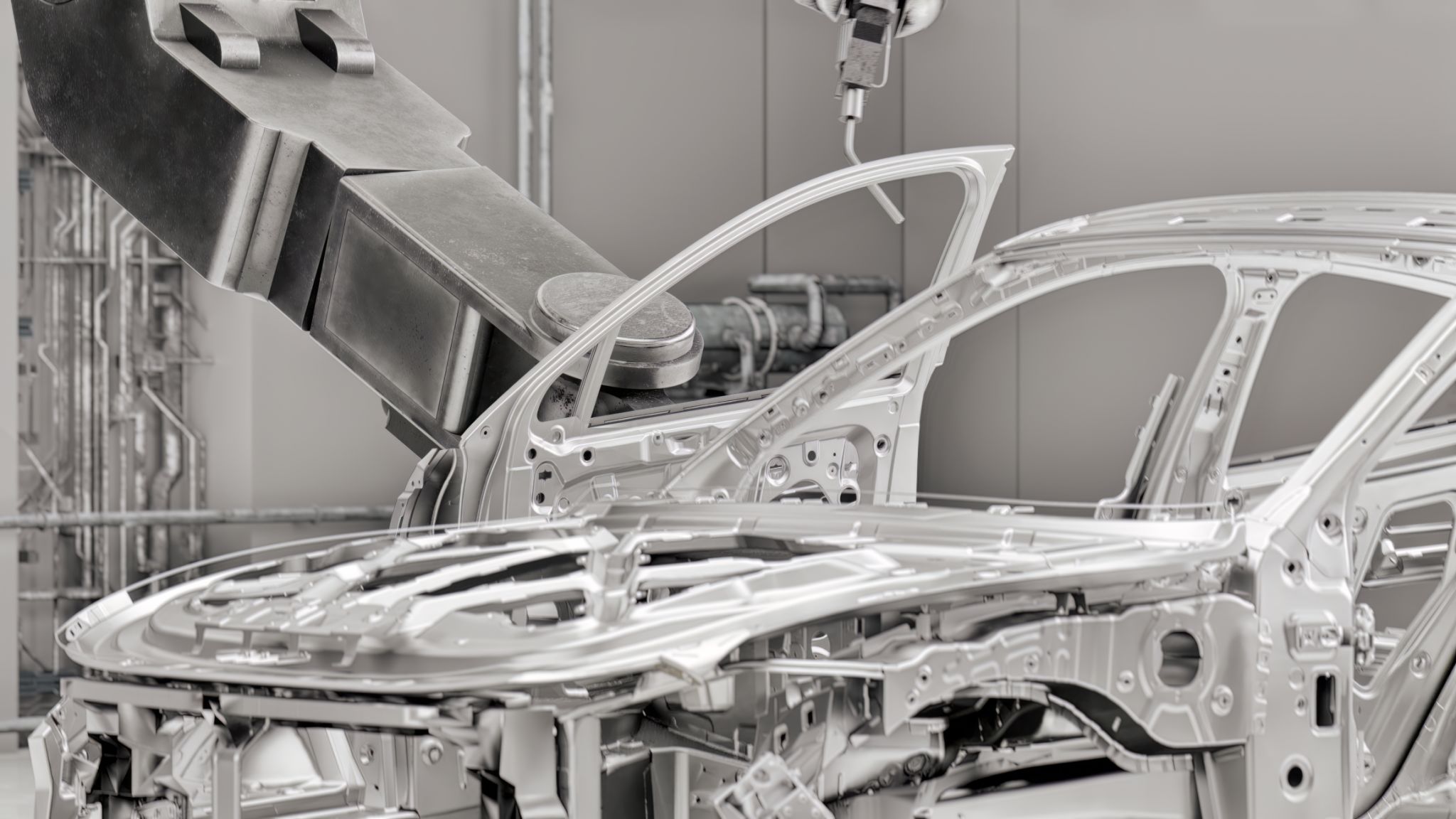
According to research organization Strategy Analytics, by 2029, more than 25% of electric vehicles in the world will adopt an Mega die Casting architecture, and the application rate in the Chinese market is expected to exceed 30%. This shows that the penetration rate of Mega die Casting in the field of automotive die-casting will continue to rise.
Far-reaching impact on the die-casting industry
The promotion of Mega die Casting brings new challenges and opportunities to the entire die-casting industry. First, the demand for die-casting equipment has been upgraded. 9,000-ton super-large die-casting machines, mold temperature control, vacuum systems, etc. all need to be updated. Secondly, the complexity of mold design has increased significantly. Due to the large wall thickness variation and long flow distance of large die castings, traditional mold manufacturing and cooling processes are difficult to cope with, and must rely on advanced CAE simulation and high-precision processing technology.
In addition, integrated die casting requires extremely high material performance and quality consistency. Most companies choose to use high-ductility aluminum alloy materials (such as Aural series, ADC12 upgraded version), and put forward higher standards for smelting and degassing processes. As automotive die casting gradually extends to structural parts and key bearing parts, material research and development and casting process synchronization iteration have also become the core competitiveness of die casting manufacturers.
Reshaping the supply chain and production methods
While simplifying the manufacturing process, integrated die casting also breaks the original parts supply ecology. Tier 1 suppliers face the risk of functional modules being integrated and must transform to system development and integration capabilities to maintain competitiveness. At the same time, the vertical integration trend of vehicle manufacturers in die casting, molds, testing and other links has increased, and the requirements for core process control have been greatly improved.
According to an industry survey published by China Diecasting, among the leading vehicle manufacturers that have implemented Mega die Casting, the average number of parts has been reduced by 40%-60%, labor costs have dropped by 20%-30%, the supply chain level has been compressed by up to two levels, and the space efficiency of a single vehicle in the manufacturing plant has increased by more than 50%.
Conclusion
Mega die Casting is not only an innovation in structural technology, but also a reconstruction of manufacturing concepts, production line layout and supply chain logic. For die-casting companies, this is a window period for industrial transition and an important gateway to determining future survival and growth.
SHD Precision Diecasting has extensive experience in large-scale die casting manufacturing and can provide automotive Mega die casting customers with integrated solutions from mold design, material selection to mass production. Relying on advanced large-scale die casting equipment and strict quality control system, we are committed to helping customers accelerate product development, optimize cost structure, and meet the higher requirements of precision and strength of the new generation of automotive structural parts.