Gravity Die Casting: Reliable Solutions for High-Precision Metal Parts
Gravity die casting is one of the most trusted and widely used metal casting methods for manufacturing medium to high-volume precision components. As industries demand stronger, more dimensionally stable, and cost-effective parts, gravity die casting continues to deliver consistent performance—particularly for aluminum and other non-ferrous alloys.
This article explains how the gravity die casting process works, its advantages, ideal applications, and why it remains a popular choice among OEM manufacturers.
What is Gravity Die Casting?
Gravity die casting—also known as permanent mold casting—is a metal casting process in which molten metal is poured into a reusable steel or iron mold under the influence of gravity alone, without external pressure or vacuum.
The mold, usually pre-heated and coated with a refractory layer, allows molten metal to fill the cavity smoothly, and solidify under controlled cooling conditions. This method is particularly well-suited for metals like:
-Aluminum alloys
-Magnesium alloys
-Copper-based alloys
Unlike sand casting, gravity die casting uses metal molds, which offer better dimensional control and surface finish. Unlike high-pressure die casting, it does not require complex machines or extremely high injection pressure, making it cost-effective for medium-run production with high quality.
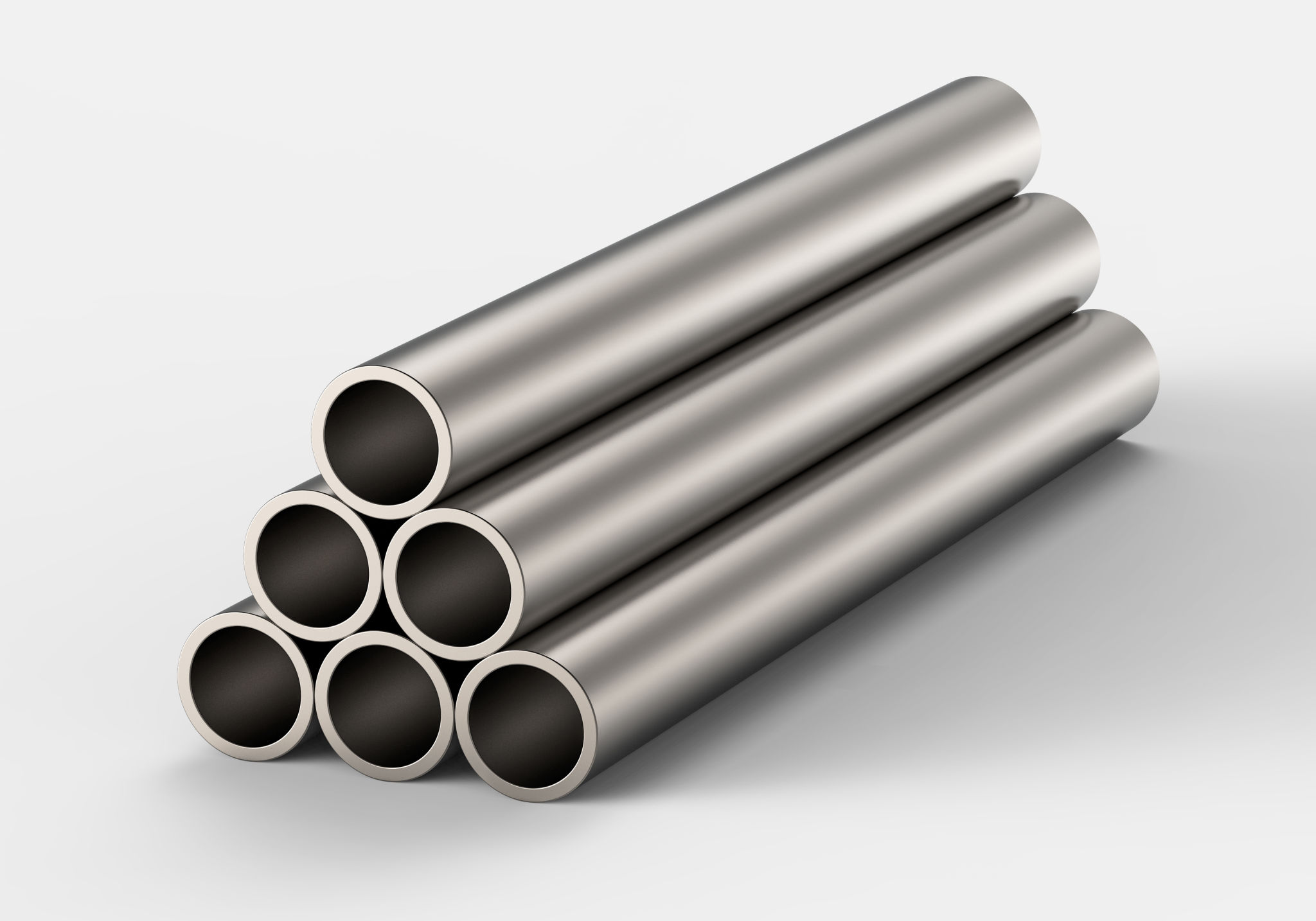
Advantages of Gravity Die Casting
Gravity die casting offers multiple benefits for manufacturers requiring both performance and consistency:
1. Superior Mechanical Properties
Parts made with gravity die casting generally have fewer internal voids and better grain structure compared to sand-cast parts. This results in higher tensile strength, fatigue resistance, and structural integrity—especially when combined with proper thermal treatment.
2. Dimensional Accuracy
Gravity die castings typically achieve better dimensional precision than sand castings. Tolerances of ±0.1mm or better are achievable with high-quality molds and controlled pouring processes.
3. Excellent Surface Finish
Gravity cast parts require minimal machining thanks to smoother surfaces and clean casting edges. Typical surface roughness can range from Ra 3.2 to Ra 6.3μm, depending on alloy and mould condition.
4. Reusable Molds
Since permanent molds can be used for thousands of cycles, this method supports cost-efficient mid- to high-volume production. The use of automated pouring and controlled cooling further improves repeatability.
Common Applications of Gravity Die Casting
Gravity die casting is widely adopted in the following industries:
Automotive: Engine brackets, cylinder heads, suspension parts, housings
Aerospace: Lightweight structural components, brackets, heat sinks
Industrial Machinery: Gearboxes, pump housings, valve bodies
Lighting & Electronics: LED heat sinks, enclosures
Smart Appliances: Coffee machine frames, induction cooker housings
The method’s balance of strength, precision, and cost-efficiency makes it ideal for components requiring mechanical performance and consistent form.
Suitable Materials for Gravity Die Casting
The most commonly used materials in gravity die casting include:
Aluminum alloys (e.g., A356, ADC12) – excellent for lightweight and corrosion-resistant parts
Magnesium alloys (e.g., AZ91D) – ultra-lightweight with good dimensional stability
Brass and bronze – ideal for decorative and corrosion-resistant components
Copper-based alloys – used for fittings and conductive applications
Material selection depends on mechanical requirements, conductivity, corrosion resistance, and intended usage environment.
Partner with SHD Precision Diecasting for Gravity Casting Projects
At SHD Precision Diecasting, we provide professional gravity die casting services for clients across the automotive, consumer electronics, lighting, and industrial equipment sectors. With precision-machined steel molds, strict process control, and expert finishing capabilities, we deliver:
-high tolerant aluminum and magnesium parts
-In-house CNC machining and surface treatment
-Scalable production from prototypes to volume runs
Whether you're developing heat-dissipating enclosures or high-strength mechanical parts, our experienced team ensures every casting meets your requirements.