5 Die Casting Mold Life Hacks: Industry Secrets to Cut Costs by 40%
Why Die Casting Mold Life Matters More Than You Think
In the global die casting industry, mold failures are responsible for nearly 60% of unexpected production stoppages, significantly impacting delivery timelines and operating costs. According to industry surveys, the average lifespan of a standard aluminum die casting mold ranges from 50,000 to 100,000 shots, but poor maintenance and suboptimal design can reduce that by up to 40%.
This decline in die casting mold life leads to soaring costs—retooling alone can cost $10,000 to $50,000 per mold, not including the productivity losses. In competitive sectors like automotive and consumer electronics, a single day of halted production due to mold failure can cause six-figure losses.
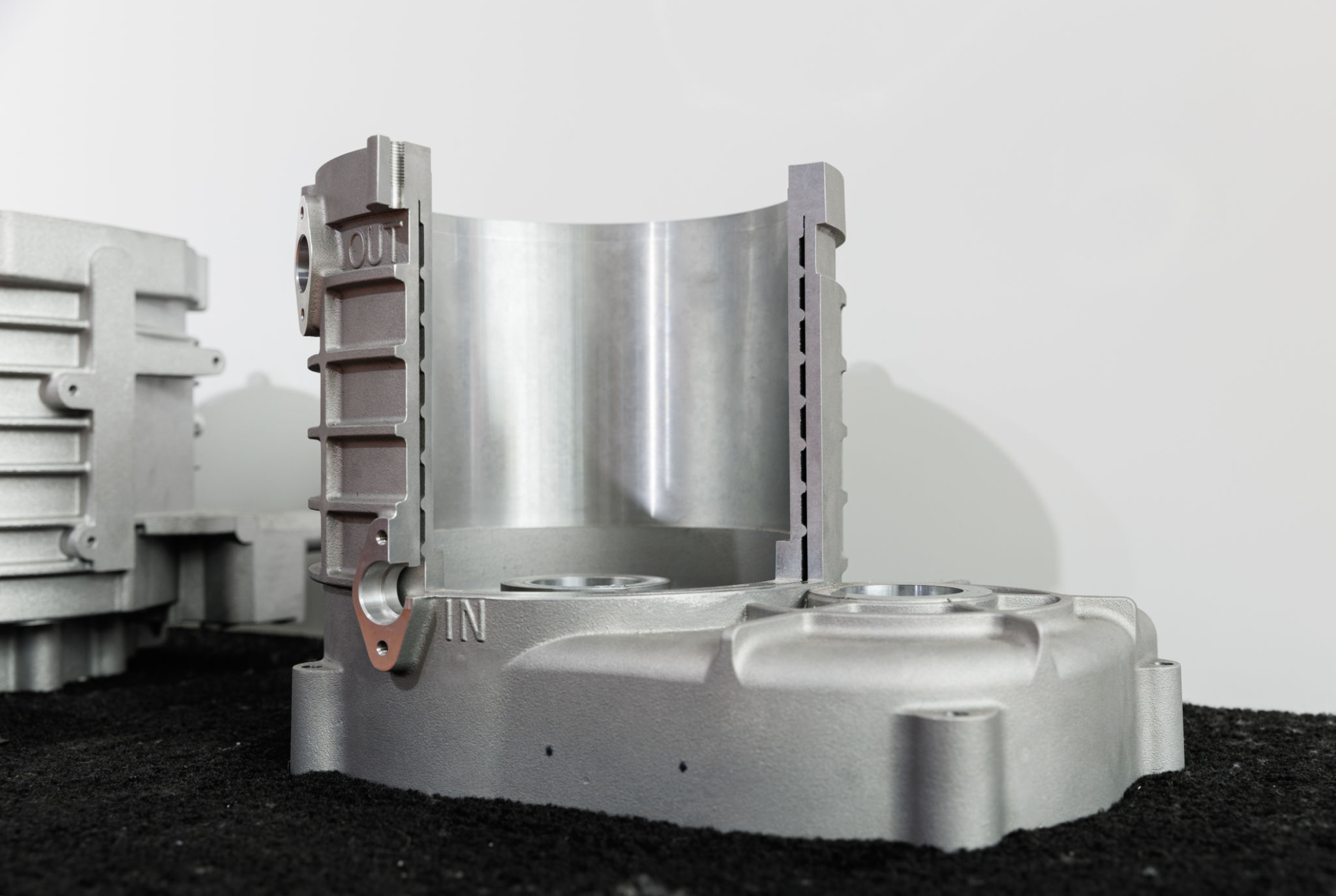
In extreme cases, small and mid-sized suppliers have been forced out of contracts—or even out of business—due to their inability to meet delivery deadlines caused by mold wear and premature breakdowns. That’s why mastering mold longevity isn't just about efficiency—it's about survival in a high-pressure market. As can be seen, Die casting dies are the backbone of high-volume production, but premature failure can severely impact efficiency and profitability. By implementing the following 5 proven strategies, manufacturers have the opportunity to extend mold life by up to 50%, reduce downtime, and reduce costs by 40%.
1. Optimize Temperature Control
Mold temperature directly impacts defect rates and longevity. Overheating accelerates wear, while uneven cooling causes thermal stress cracks.
Target Ranges:
Zinc alloys: 150–220°C (preheating) & 80–120°C (operating) 3
Aluminum: 200–300°C (preheating) & 180–250°C (operating)
Tools: Use infrared thermography to monitor hotspots and adjust cooling channels.
2. Select High-Performance Materials
Not all tool steels are created equal. For high-pressure die casting (HPDC), prioritize:
H13 Steel: Balances toughness and heat resistance.
Surface Coatings: Titanium nitride (TiN) or diamond-like carbon (DLC) coatings reduce friction and prevent soldering.
Case Study: A German automaker increased mold cycles by 35% using DLC coatings on aluminum die casting molds.
3. Implement Predictive Maintenance
Unplanned repairs can be three to five times more expensive than proactive maintenance, making scheduled upkeep essential for cost control and operational stability.
Daily: Lubricate ejector pins and check alignment.
Monthly: Inspect for micro-cracks via dye penetrant testing.
Annually: Re-machine worn surfaces to restore tolerances.
4. Optimize Ejection Systems
Sticking parts cause 30% of mold damage. Solutions include:
Draft Angles: Ensure 1–3° draft for smooth ejection.
Ejector Pin Lubricants: Use high-temp graphite-based lubricants.
Sensor Integration: Install force sensors to detect abnormal ejection resistance.
5. Train Operators on Best Practices
Human error accounts for 15% of mold failures. Focus on:
Proper Handling: Avoid mechanical shocks during mold changes.
Cleaning Protocols: Remove residues with ultrasonic cleaning, not abrasive tools.
Conclusion
Extending die casting mold life isn’t just about technology—it’s a strategic balance of material science, process control, and workforce training. By adopting these 5 hacks, manufacturers can achieve:
✅ 40–50% longer mold lifespan
✅ 30% reduction in defect-related scrap
✅ 10k–50k annual cost savings per mold
SHD Precision Diecasting is a professional OEM manufacturer of die casting services. Whether it is high pressure die casting or semi-solid die casting services, our service and production teams can guarantee the life of the mold and daily maintenance work, ensuring that perfect products can be processed in the shortest delivery time when customers need them.
We sincerely encourage you to contact us and cooperate with us to create corporate success together.